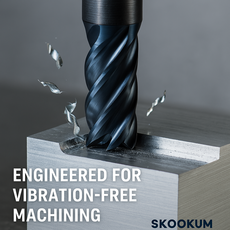
In the world of precision machining, few issues are as persistent—or as misunderstood—as chatter. Whether you’re a seasoned CNC programmer or a shop owner looking to get more life out of your tools, mastering how to control vibration in milling can save serious time, money, and frustration.
At Skookum End Mills, we design tools that tackle the problem from the ground up, helping you achieve smoother finishes, longer tool life, and more reliable results with every cut.
What Is Chatter in Milling?
Chatter refers to the unwanted vibration that occurs between the cutting tool and the workpiece during machining. Often triggered by harmonic resonance, chatter can:
-
Produce noisy, erratic cuts
-
Damage your tool or workpiece
-
Shorten machine life
-
Create uneven or marked surfaces
-
Disrupt dimensional tolerances
If you’ve ever heard that “screeching” sound while roughing or seen ripple marks on your finish, you’ve seen chatter in action.
How Skookum End Mills Help Prevent Chatter
Chatter isn’t just caused by operator error or loose setups—it can start with the tool itself. That’s why every Skookum end mill is developed with cutting-edge design features aimed at suppressing vibration before it begins.
Precision Ground Geometry
We don’t just grind to spec—we grind for performance. Our geometries are optimized to reduce cutting pressure and promote smooth, stable chip flow.
Variable Helix & Pitch Designs
By varying the angle and spacing of each flute, our end mills avoid the “synchronized impact” that causes vibration to build up. The result? Quieter, cleaner cuts.
Tool Rigidity
With shorter lengths of cut and reinforced shanks available, Skookum end mills maintain optimal rigidity—especially important for deep pockets and long-reach applications.
Material-Specific Designs
From aluminum to hardened tool steels, our tooling is tailored to your material, minimizing excess force and chatter with the right rake angles, coatings, and flute styles.
Chatter Reduction Is About the Whole Setup
While your end mill plays a major role, the entire cutting system matters. If you’re experiencing vibration, consider:
-
Tool Holders: Use high-precision holders with minimal runout (hydraulic or shrink-fit recommended).
-
Machine Maintenance: Worn bearings or spindle misalignment can amplify vibration.
-
Workholding: Always aim for maximum part rigidity with minimal overhang.
-
Toolpath Strategy: Constant cutter engagement and optimized feeds can drastically reduce resonance.
Real-World Results: Less Chatter, More Output
Shops using Skookum Tools consistently report improvements in:
✔️ Surface finish consistency
✔️ Cycle time reduction
✔️ Tool longevity
✔️ Dimensional accuracy
✔️ Operator confidence
Whether you're machining aerospace-grade alloys or batch-running production parts, the stability and efficiency of your cuts can make or break your margins.
Choosing the Right Skookum End Mill
Our product range includes:
-
Performance Series: Advanced geometry for tougher materials and aggressive machining
-
Aluminum Series: Mirror-polished flutes, high rake, and superior chip evacuation
-
Miniature & Micro Tools: For fine feature work and tight tolerance applications
-
Long Reach / Reduced Neck Tools: Engineered for access and rigidity in deep cavities
Use our End Mill Selector Tool to find the perfect cutter for your application.
The Bottom Line: Built for Balance, Designed for Results
Machining doesn’t have to be a balancing act between speed and quality. With Skookum End Mills, you get both. Our tools are precision-built to control vibration and deliver clean, reliable performance cut after cut.
Ready to make your next job smoother and more stable?
Explore our full line at SkookumEndMills.com, or reach out to our team for expert recommendations.